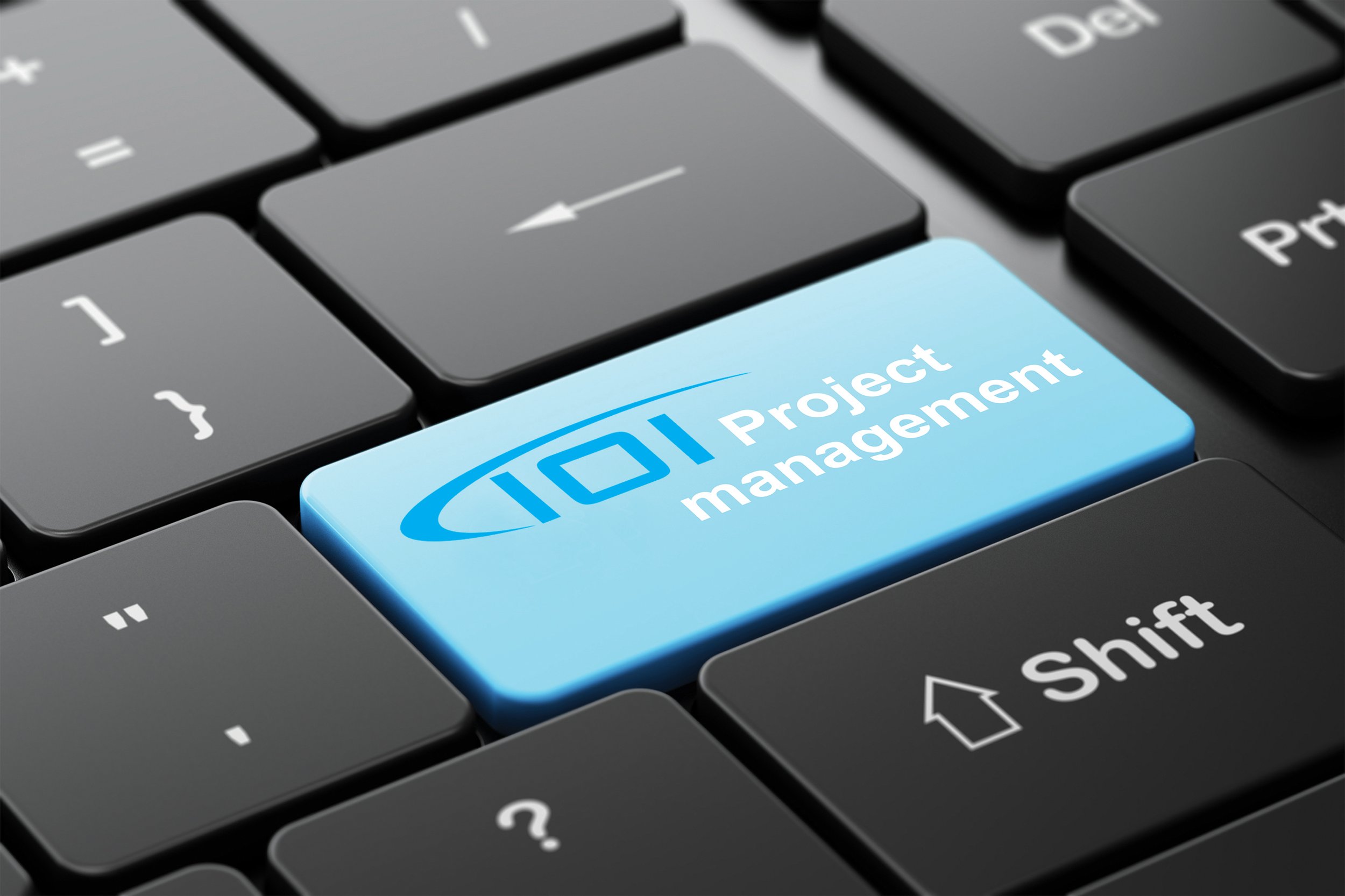

Cause, Effect, Outcome.
Our Typical Project Execution Expertise
Upstream Asset Transfer Permian Basin, TX
Charged with Integration of upstream production wells to Client requirements and acceptable risks on transitioning acquisition of upstream oil and gas production assets to the purchasing company’s standards and applications. Accomplished by client consulting, information gathering, SCADA integration, enterprise OSI PI integration, privatized cell network, and disaster recovery design and implementation. A successful outcome based on mechanical design utilizing best practice and integrity experience, operational knowledge, safety promotion, GIS, and working knowledge of AutoCAD. The project led to a three (3) year contract with the acquisition client.
Cloud-Based Oil Midstream Pipeline SCADA Implementation
Consulted, designed, and built Mid-Stream Operational SCADA and measurement collection system for a new 100-mile venture Mid-Stream pipeline using Ignition as the host software and MS Azure hosting platform. Utilized alarm rationalization and delivery schedule for measurement collection and troubleshooting. SCADA system added transferable value to Mid-Stream pipeline company at the sale of the asset.
Natural Gas Compressor, Processing Plant Automation, and Commissioning
We have completed many turnaround automation plant projects from PLC to HMI to Commissioning of Mid-Stream and Down-Stream compressor and processing plants. Successful completions included reciprocal and turbine compressors, Cryo plants, Processing plant with networking, safety systems, processing systems cause, effect, alarm rationalization, control room design, and commissioning compliance with best practice safety implementation along with client requirements utilizing best operating practice and technique.
Control Room Design, PHMSA Compliance, and PHMSA Audit and Audit Attendance with Client
In conjunction with the client to redesign two control rooms approximately 1000 miles apart, redesigned two control rooms for downstream interstate pipelines in their area for PHMSA compliance. Each control location servers were utilized as a backup of the other control room using VMware and VMware sync software. Screens redone for efficiency, point to point qualifications of screens, alarm rationalization and removal of nuisance alarm removal, client education and selection of safety-critical points, PHMSA compliant control room manual updates and added procedures, custom-written control room note application, shift studies, and successful completion of three state PHMSA audit.